Polyurethane: The Backbone of Prefabricated Building Innovation
In the rapidly advancing construction industry, prefabricated buildings are becoming the epitome of efficiency, sustainability, and precision. At the core of this innovation lies a material that has redefined construction standards: polyurethane. Known for its unmatched versatility, polyurethane has transformed prefabrication by offering superior insulation, structural support, and durability. Whether it’s sealing joints, enhancing energy efficiency, or creating lightweight yet robust panels, polyurethane is the unsung hero driving prefab construction forward.
This blog delves deep into the role of polyurethane in prefabricated buildings, exploring its benefits, applications, and why it is integral to modern construction.
What is Polyurethane?
Polyurethane (PU) is a highly adaptable polymer created by reacting polyols with diisocyanates. Developed in the mid-20th century, polyurethane can be tailored into a variety of forms:
Rigid Foam
Flexible Foam
Adhesives and Sealants
Elastomers
Coatings
Expanding Foam
For construction, rigid polyurethane foam (RPUF) and expanding polyurethane foam are the most prominent forms due to their high thermal resistance, lightweight properties, and durability. These materials offer unparalleled advantages for prefabricated buildings, making them the preferred choices for applications such as insulation, bonding, sealing, and structural support.
Why is Polyurethane Essential for Prefabricated Buildings?
Prefabricated buildings are characterized by their speed of construction, precision in assembly, and commitment to sustainability. Polyurethane perfectly aligns with these goals, offering critical benefits:
1. Superior Thermal Insulation
Rigid polyurethane foam boasts one of the highest R-values (thermal resistance) per inch, making it a highly efficient insulating material.Expanding foam ensures even the smallest gaps and irregular spaces are filled, eliminating thermal bridges.Prefab structures with polyurethane insulation meet stringent energy efficiency standards and contribute to reduced greenhouse gas emissions.
2. Lightweight Yet Strong
Polyurethane foam’s low density makes it ideal for lightweight prefab panels, facilitating easier transportation and assembly.Despite being lightweight, it provides structural stability, supporting the integrity of walls, roofs, and floors.
3. Moisture and Mold Resistance
Polyurethane, including expanding foam, resists water penetration, preventing issues like mold and mildew growth.This quality ensures prefab buildings remain durable and hygienic, even in humid or wet environments.
4. Durability
Prefab buildings made with polyurethane are resistant to wear and tear, pests, and extreme weather conditions.This longevity reduces maintenance costs and extends the lifespan of the structure.
5. Speed of Application
Expanding foam and polyurethane-based adhesives accelerate the sealing, bonding, and insulation of prefab components, cutting down on construction time.
Applications of Polyurethane in Prefabricated Buildings
1. Insulated Wall and Roof Panels
Rigid polyurethane foam is commonly used as the core material in sandwich panels, a staple of prefab construction.Expanding foam is also used to fill cavities and reinforce thermal insulation in these panels.
Structure:
Outer Layers: Made from materials like steel, aluminum, or fiber cement for structural integrity.
Core Layer: Polyurethane foam or expanding foam provides lightweight strength and thermal insulation.
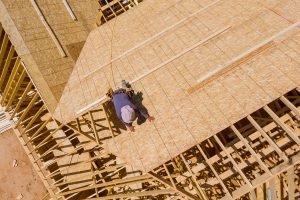
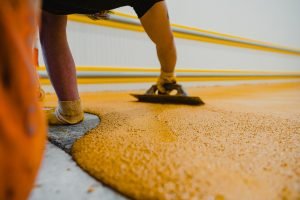
2. Floor Insulation
Prefabricated floors often incorporate polyurethane foam for enhanced thermal and acoustic insulation.Expanding foam can be used to fill voids and ensure a seamless, insulated foundation.This helps reduce noise transfer and improves the overall energy efficiency of prefab units.
3. HVAC and Pipe Insulation
Polyurethane foam is extensively used in insulating HVAC systems and pipes within prefab buildings.Expanding foam is particularly effective for irregularly shaped areas, creating a custom-fit barrier that prevents heat loss and condensation.
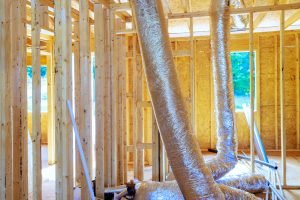

4. Sealing Prefab Joints
Expanding polyurethane foam is ideal for sealing gaps, joints, and seams between prefab components.Its ability to expand and conform to any space ensures a tight, airtight, and watertight seal.This prevents energy loss, moisture intrusion, and noise leakage in prefab structures.
5. Bonding and Adhesion
Polyurethane adhesives are used to securely bond prefabricated components, ensuring precision and stability.These adhesives allow for thermal expansion and contraction while protecting the underlying structure of the building.
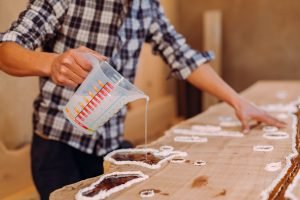
Advantages of Using Expanding Foam in Prefab Construction
1.Efficient Insulation:
It expands to fill even the smallest crevices, eliminating air leaks and providing superior thermal insulation.
2.Lightweight and Durable:
Once cured, it forms a lightweight yet sturdy structure that enhances prefab unit durability without adding significant weight.
3.Ease of Application:
Expanding foam is quick to apply, cures fast, and adapts to irregular shapes, making it perfect for the precise demands of prefabricated construction.
4.Versatility:
Available in low-expansion formulations for delicate applications or high-expansion versions for larger gaps and cavities.
Polyurethane in Action: Sandwich Panels
One of the most prominent uses of polyurethane in prefab construction is in sandwich panels. These panels are critical for walls, roofs, and partitions, offering a combination of strength, insulation, and ease of installation.
Structure of Sandwich Panels:
-
Outer Layers: Made of steel, aluminum, or wood for durability.
-
Core Layer: Rigid polyurethane foam or expanding foam provides lightweight strength and excellent thermal performance.
Benefits of Sandwich Panels:
-
Thermal Efficiency: Keeps interiors cool in summer and warm in winter.
-
Resistance: Protects against moisture, fire, and pests.
-
Lightweight Design: Simplifies transportation and assembly.
Challenges and Solutions
1. Environmental Impact
Challenge: Traditional polyurethane production relies on petroleum-based chemicals, contributing to environmental concerns.
Solution: Innovations in bio-based polyurethane and improved recycling techniques are addressing this issue, making polyurethane production more sustainable.
2. Cost
Challenge: High-performance polyurethane foam may have a higher upfront cost than traditional materials.
Solution: The long-term energy savings and reduced maintenance costs make polyurethane a cost-effective investment for prefab buildings.
Polyurethane and Prefabrication: A Perfect Partnership
The integration of expanding polyurethane foam further cements polyurethane’s role in prefabricated buildings. Its ability to provide seamless sealing, adaptable insulation, and precision fit is a perfect match for the demands of prefab construction, where efficiency and sustainability are critical.
Here’s why this partnership works:
Speed:Expanding foam accelerates prefab assembly by ensuring airtight, watertight, and insulated connections.
Precision: Tailored formulations and the foam’s expanding nature ensure consistent quality across prefab components.
Sustainability: Combining expanding foam’s energy efficiency with prefab’s resource optimization reduces the overall carbon footprint.
Conclusion
Polyurethane, including expanding foam, is a cornerstone of prefabricated construction, enabling builders to achieve faster, more sustainable, and more efficient outcomes. From sandwich panels to HVAC insulation and joint sealing, its versatility and performance make it indispensable in modern building systems. As prefab construction continues to grow, polyurethane will play an even greater role in shaping the future of smart, sustainable building practices.
If you’re exploring the potential of prefabricated buildings, polyurethane—rigid foam and expanding foam alike—should be at the top of your material considerations. Discover how this innovative material is transforming construction by checking out our related blog on prefab construction. Together, polyurethane and prefab technology are leading the way toward a more sustainable and efficient construction industry.